Robotic process automation (RPA) is a critical tool for optimizing standardized process activities and data aggregation in procurement. Organizations across industries have leveraged RPA to drive productivity gains, feed data-driven decision making and enable procurement staff to focus on higher-value work. Yet this tool needs to be applied thoughtfully and to the right processes to be effective. Drawing from APQC’s Open Standards Benchmarking data and its Sourcing and Procurement Blueprint for Success report, here’s how RPA can benefit procurement and help organizations get the most from this tool.
Leverage process automation for productivity gains
RPA is a form of process automation that can handle repetitive, transactional, rules-based tasks that require little or no human oversight. By taking over the performance of routine and highly manual tasks, RPA frees time for humans to focus on work that truly drives value and innovation in procurement and beyond.
There are at least four reasons why RPA is a compelling option to automate procurement processes:
RPA is a form of process automation that can handle repetitive, transactional, rules-based tasks that require little or no human oversight. By taking over the performance of routine and highly manual tasks, RPA frees time for humans to focus on work that truly drives value and innovation in procurement and beyond.
There are at least four reasons why RPA is a compelling option to automate procurement processes:
- RPA is quicker and cheaper to implement than many ERP projects (and requires less IT support).
- RPA provides an ROI of 30-200% in its first year.
- Chatbots can handle complex verbal information.
- RPA allows organizations to shift focus to more valuable procurement activities while eliminating errors from transactional work.
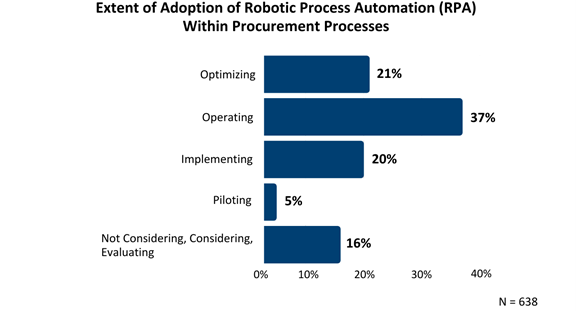
By taking over the performance of routine and highly manual tasks, RPA frees time for humans to focus on work that truly drives value and innovation in procurement and beyond. – APQC
Despite these benefits, APQC has found that, when it comes to RPA, many organizations have room for further growth. For example, only 21% of organizations have fully optimized RPA for procurement processes, and 37% have processes that are operating but not optimized. The momentum is certainly moving toward greater automation in procurement; only 16% of organizations are not considering it at all at this point.
APQC’s research confirms that RPA technology improves procurement efficiency for the organizations that invest in optimizing it. For example, organizations that have fully optimized RPA for procurement processes have 84 full-time equivalents (FTEs) ordering materials and services per $1 billion purchases (at the median), whereas those with no RPA in place require 143 FTEs.
Automate appropriately
RPA is not a plug-and-play tool and must be set up with care. With a thorough understanding of how end-to-end processes work, organizations will need to select appropriate processes or activities for automation using standardized criteria. Evolving, emerging or immature processes—and those with large ratios of exception management—will not be good candidates for automation. More broadly, sophisticated RPA applications will require ongoing adjustment, and procurement roles may need to be restructured in order to fully realize productivity gains from RPA.
While it completes routine work faster and at a higher quality, RPA can also make mistakes faster if given bad data. Poor data quality or the insufficient definition of business rules can lead, for example, to RPA ordering the wrong parts fast and in large quantities. The quality of RPA, especially when incorporating artificial intelligence (AI) capabilities, will largely be a product of the maturity of the organization’s data management efforts.
Another word of caution is in order — there is a point of diminishing gains and even productivity losses depending on the number of bots that procurement is using. It makes sense that a procurement team would add additional bots as it grows its RPA capabilities. For instance, 35% of organizations that are optimizing the use of RPA have more than 20 bots. Yet APQC finds that gains from RPA begin to reverse at this point. For example, organizations employing more than 20 bots have more FTEs ordering materials and services and process fewer purchase orders per FTE than those that use 6-20 bots. Similar productivity losses occur for those organizations that have bots operating but not necessarily optimized.
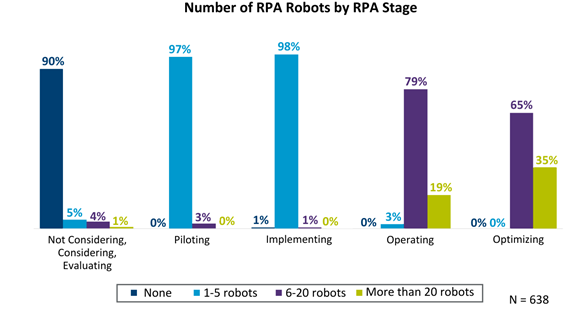
There is a point of diminishing gains and even productivity losses depending on the number of bots that procurement is using. – APQC
It is likely that these organizations are seeing declining results because they are automating processes that are not actually good candidates for RPA. Some procurement processes are highly strategic and require critical thinking and relationship building. For that reason, procurement needs to be intentional and selective about what it is automating. RPA might be a hammer when it comes to cutting costs and boosting efficiency, but not every process is a nail.
Conclusion
When implemented well, RPA can empower procurement teams to work with greater efficiency and productivity in core procurement processes. RPA also frees procurement staff from highly manual activities and allows them to focus on more value-added tasks that only humans can perform like supplier relationship management or strategic planning. Like any tool, however, RPA is only as effective as its inputs, and it isn’t always the right tool to use. Approaching RPA strategically and with care helps ensure that automation gains are substantive and that the tool solves problems rather than creating them.